Motorsport photo
The NASCAR season kicked off this year with a race at the historic Bowman Gray Stadium, which had not seen a NASCAR Cup Series race since 1971. While the parking lot paddock behind the fieldhouse hearkened back to those early days of stock car racing, some 40-plus years before, the cars in the garage that day were far from those that might have been assembled in the backyard garages of the 1970s.
Advertisement
The differences were further apparent in my time spent with Hendrick Motorsports just a few days later. Entering a shop on the Hendrick campus already feels like being granted access to NASA’s production facility — complete with pristine epoxy floors and stainless steel plates laid out for car assembly (rather than rockets). And as you travel deeper into the shop you’ll find the metrology lab which houses an array of robots that are measuring the best parts for a car down to the thousandths (0.000) for use in their next set of cars for the next race.
You quickly realize building a race car is almost like building a rocket, all to find what little bit of an advantage you can gain against your opponents and rivals.
Building rockets… on wheels
Around 85% of the parts that are used to build a NASCAR Cup car must come from a single-source supplier. Teams are required to use these parts as-delivered from the supplier. However, they are allowed to choose how they combine parts during assembly and this is where performance gains can be found.
Advertisement
According to Hendrick Motorsports vice president of competition Chad Knaus, this is key to finding speed.
“They want to have a set of tolerances that everybody has to operate within and it’s up to us to take those tolerances, stack them up in a way that creates performance, whatever that metric may be that we determine is the most important performance enhancer for that track and apply it. Whether that be weight, whether that be geometry, whether that be shape. There’s a million ways to do that and each race track is unique in which one you need to apply or how you need to apply it and we do that with all of this Hexagon equipment that we’re very fortunate to have.”
For instance, each NASCAR car number is allotted a set of primary chassis pieces: seven center sections, ten front clips, and ten rear clips. So, a four car team like Hendrick Motorsports, has to keep up with measurements for over a hundred of these pieces and how all of the other individual components that bolts to them will stack up. That’s where Knaus sees the biggest efficiencies in using some of this automated measuring equipment.
“It helps us predict where we feel like geometry will be once we put the components together and then after we put the components together we can go back and reaffirm that our math meets reality. We do that with every single car, every single week, so the task as you can imagine is pretty daunting.”
One of Hendrick’s team members demonstrates Hexagon’s Absolute Arm
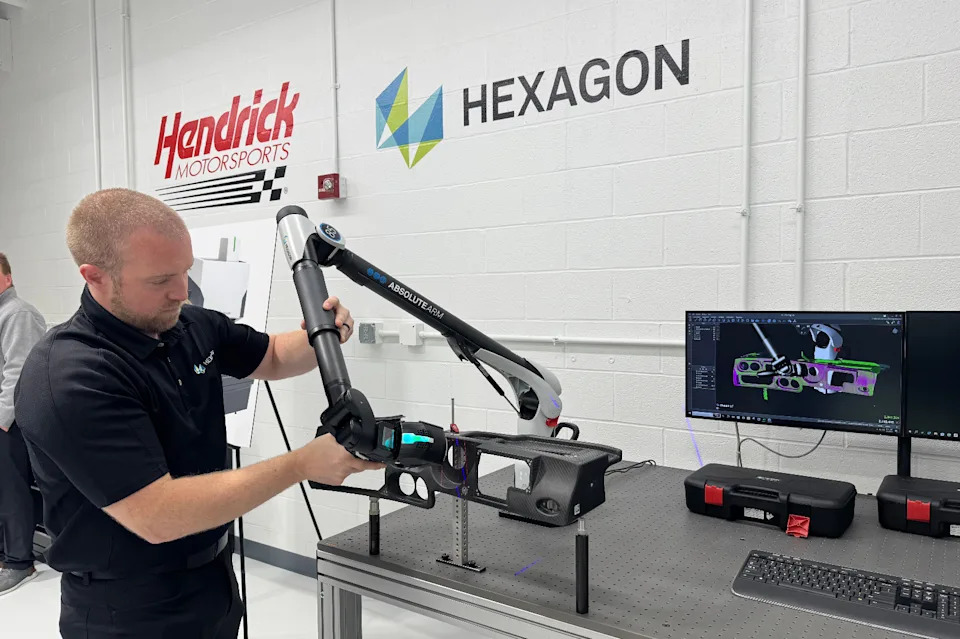
One of Hendrick’s team members demonstrates Hexagon’s Absolute ArmBozi Tatarevic
Bozi Tatarevic
Advertisement
Measuring these parts starts out with Hexagon, a company that specifically builds robots for these types of endeavors, and its Absolute Arm — a flexible device that a technician can use to create an accurate CAD model of any given part using touch probing and laser scanning. Large parts like the center section are probed and scanned as soon as they come in and added to their parts database. NASCAR allows for a tolerance of 0.150 inches in their at-track inspection scans. Hendrick is able to achieve an accuracy of under 0.010 inches in their shop scans and that room is what allows them to assemble parts right on the edge of rules to maximize performance.
But the real efficiencies show up once we get deeper into the shop, at the metrology lab. This newly launched lab is equipped with robotic scanners that require very little intervention and can scan components like suspension uprights or brackets automatically.
A Hexagon Tempo robot with a movable arm that can pick up parts sits in one corner of their metrology lab and is loaded with drawers of control arm mounting brackets. I watch as the Tempo opens a drawer and then uses an arm to pick up one of these mounting brackets and place it on the Touch+ coordinate measuring machine (CMM) that was attached to it. The Touch+ identified the bracket and immediately grabbed a probe from its side and started measuring.
The Hexagon Touch+ in action measuring one of the Hendrick Motorsports’ parts.
The Hexagon Touch+ in action measuring one of the Hendrick Motorsports’ parts.Bozi Tatarevic
Bozi Tatarevic
A closer view of the part being probed by the Hexagon Touch+ robot for measurements
A closer view of the part being probed by the Hexagon Touch+ robot for measurements Bozi Tatarevic
Bozi Tatarevic
Advertisement
The output from that measurement starts filling in on a nearby screen. Once the bracket iss measured, the robotic arm picks it up and places it back in the drawer. After all of the brackets in the first drawer are measured, the robotic arm closes the drawer and opens the next one. The only intervention required from a technician is loading all of the drawers earlier in the day. Once all of the brackets are measured, their dimensions are exported from the machine and into a database that feeds a variety of tools for Hendrick engineers and mechanics. The most important of those is their simulation software which allows them to build a car virtually to a specific body and suspension measurements.
From virtual to reality — a new, faster car
A couple of thousandths of an inch of difference between any of the two brackets measured from these scans, can lead to a suspension geometry that equates to speed on track.
So, those dozens of suspension mounting brackets are now available to the engineer that is virtually building a car for a specific track. All of the measured parts are pulled from the database and once the car is fully virtually built, the information can be shared with mechanics to build the real-world car.
Advertisement
Parts are identified by QR codes and serial numbers, making it easy for the mechanics to identify them. They’re tasked to assemble the cars on those large stainless steel plates where once their work is done, they will use one of the 33 Hexagon Absolute Arms around their facility to measure the assembled car and make sure it matches the virtual model. Once the entire car has been measured, the software will show any variations that are then investigated and brought up to spec (if necessary). It’s an absolutely tech-savvy approach when you realize aligning race cars was traditionally done with things like strings or lasers. But at Hendrick, they rely solely on the Absolute Arms to verify those tight tolerances. Any additional changes to the suspension are simply verified by rescanning those suspension components.
One of the drawers filled with parts to be scanned at Hendrick Motorsports.
One of the drawers filled with parts to be scanned at Hendrick Motorsports.Bozi Tatarevic
Bozi Tatarevic
Advertisement
Racing the NASCAR Next Gen car for multiple years has resulted in a collection of available parts for Hendrick and being able to accurately catalog them in their database is part of what allows them to consistently build fast cars. Not only do they catalog new parts, but they also rescan those same parts once the race cars are torn down after a race. This not only allows them to keep a large collection, but can also reveal if a part is damaged or out of tolerance after it has seen the track.
While Hendrick Motorsports has an extensive database of parts from years of scanning everything made available to them, the job isn’t over quite yet. New robotic tools, delivered last fall, have required another round of scanning. Hendrick Motorsports’ quality control supervisor Roy Crump shared with Motorsport.com during my visit, “For the last two or three months, we’ve been trying to measure as many parts as we can just to verify what we have because like I said, in the past we were using two guys to measure with the Romer arms. So, remeasuring everything we have in our inventory. Just understanding what we have now. Just to a way better degree than what we ever thought we would have. And it just helps build the confidence of what we’re putting together.”
In addition to those 33 Absolute Arms, Hendrick also uses seven CMMs and 13 scanners from Hexagon and continues to expand those capabilities with the launch of their new Hexagon Metrology Lab. With all this technology at their disposal, it’s not really surprising why a team like Hendrick does so well when it comes to race day.
Read Also:
Waiting for IndyCar tech updates? Some are already here, or coming very soon
An electrifying first look at Ford’s Mustang Mach-E NASCAR EV prototype
The new tech changing IMSA’s hotly debated “balance of performance” rules
Read the full article here